

KW Automation
In June 2015, I joined KW Automation in search of a new challenge and a change of scenery from the cold wind of Melbourne, Victoria to the warm waters of the Sunshine Coast in Queensland. KW Automation is recognised as a world leader in the design, manufacture and supply of quality horticulture and material handling equipment. However, we have also ventured into other industries such as material separation and also providing grading lines for the Oyster industry which is booming in the eastern coast of Australia.
At KW, I have continued working as a design engineer. My previous experience in designing user centric automated equipment has helped me greatly in continuing to design equipment that reduces operator interaction to a bare minimum while also ensuring that accuracy and precision is maintained.
Redback Test Services
I was part of a small team of engineers and technicians who worked together with Manufacturing, Product Development, Process and Test engineers of our client companies to develop fully/semi automated stations to be used in the manufacturing/assembly lines of their companies.
Working in a small company has its perks in that we got to work on almost all the aspects from design to delivery of the projects we were involved in. Some of the aspects I have been involved in projects we have delivered are -
-
1. Mechanical Design & Development – 3D CAD modeling, Rapid prototyping, drafting, Assembly documents
-
-
2. Pneumatics - Use of control valves, solenoids, valve banks, flow controllers, Pneumatic circuit diagrams
-
-
3. Automation - PLC programming, electro-mechanical and pneumatic actuators
-
-
4. Equipment commissioning - FAT protocols
-
-
5. Engineering documentation – Plant manuals, Operator instructions, Assembly details
-
-
6. Maintenance – remote troubleshooting, Local and interstate site visits
GlaxoSmithKline
This was my first engineering job and was a very good one at that. Working directly under the Engineering Manager, I was exposed to a wide variety of equipment used in a plant such as control valves, pumps, distillation columns, reverse osmosis filters, belt filters etc. I also played a significant role in the implementation of a CMMS (computerised maintenance management system) at the plant and was involved in their energy management program.
Below are some of the highlights of my experience at GSK -
-
1. Automated the data retrieval from plant management software
-
-
2. Was a key member in implementing CMMS (computerised maintenance management) at GSK Port Fairy
-
-
3. Automated preventative maintenance scheduling by using MS Access database and Excel
-
-
4. Performed preventative maintenance testing on vessels and other equipment
CSIRO
I got the opportunity to work with the scientists of CSIRO (Commonwealth Scientific and Industrial Reasearch Organisation) on a project to produce bio-diesel using algae. This was a fascinating project as I was already working at GSK on energy management, so combining energy production with management concurrently was very interesting.
We worked on the fluid dynamic aspects of producing the optimum conditions in the water flow for the algae to produce the most amount of lipids (fat) throughout the year 2011. My team was awarded a high distinction (HD) for the efforts we put in to this research program.
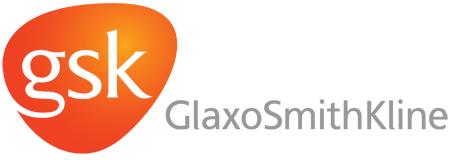


